Description
CONCENTRATED ACETONE CONCRETE DYE
Beautifully and easily color concrete in 28 awesome colors. Exterior Kolour Dye is a deep penetrating, translucent, UV stable liquid color dye for staining both interior and exterior concrete. These dyes come in a highly concentrated form that you dilute with acetone to create a ready to use product in the intensity of your choice.
Acetone Dyes are now the preferred method for coloring concrete, especially interior concrete floors. Dyes create consistent predictable colors every time, without the mess and labor associated with old-fashioned acid staining. With acetone dyes, floors can now be prepped, stained and sealed in a single day. Pick the perfect color, or mix and match to create the exact look, color and contrast you desire.
Because of their UV stability, Exterior Kolour Dyes can be used for all types of indoor and outdoor projects such as; interior floors, driveways, sidewalks, pool decks and patios. Acetone dyes must always be sealed after application to protect the colored surface. Acetone dyes can only be used on properly prepped, clean, bare and un-sealed concrete surfaces.
Kolour Dye is available in 28 awesome colors:
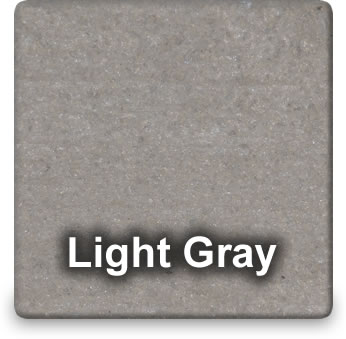
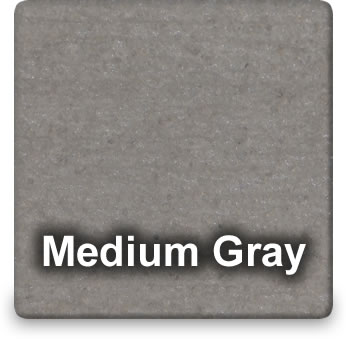
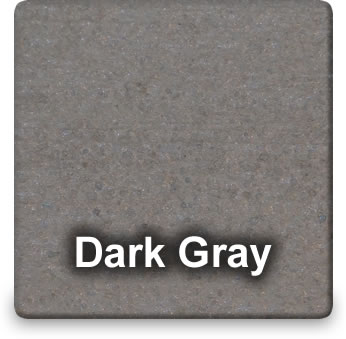
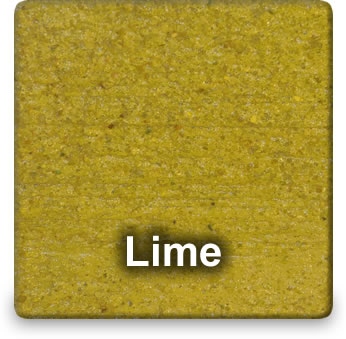
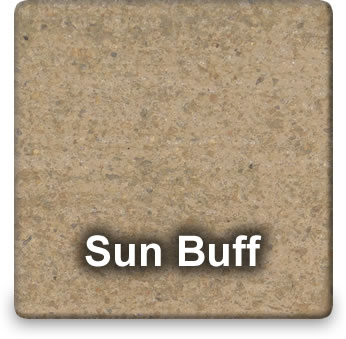
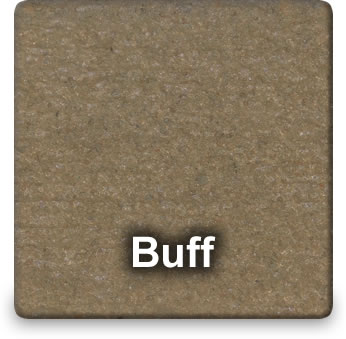
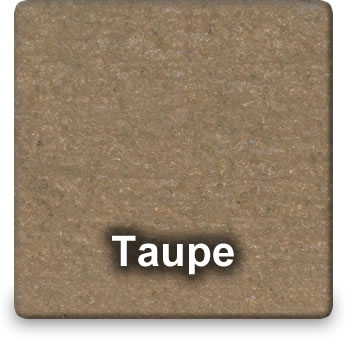
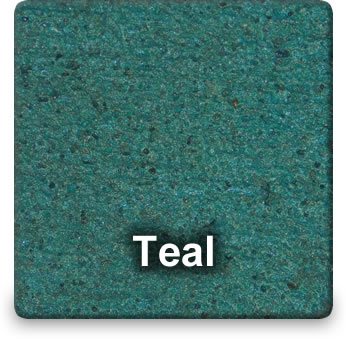
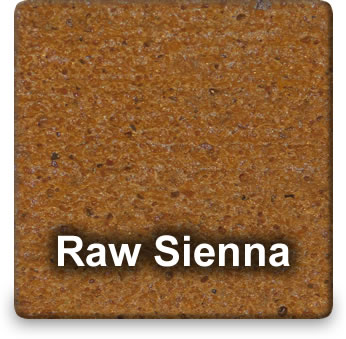
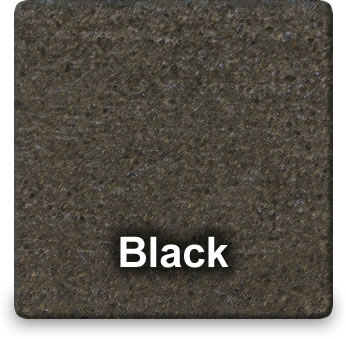
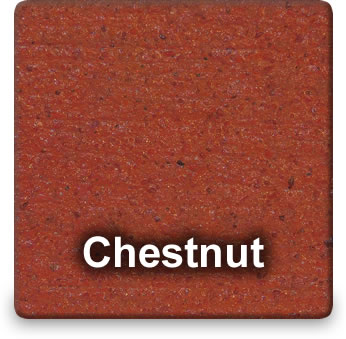
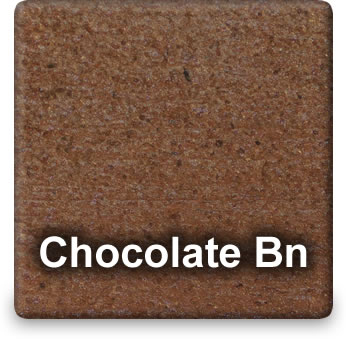
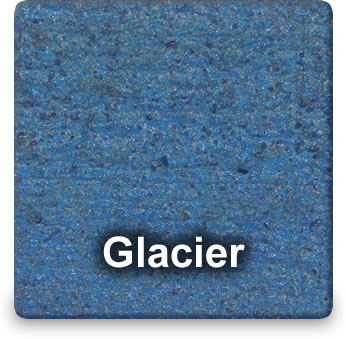
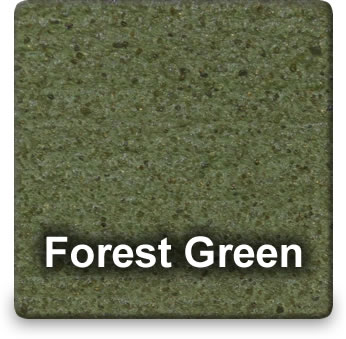
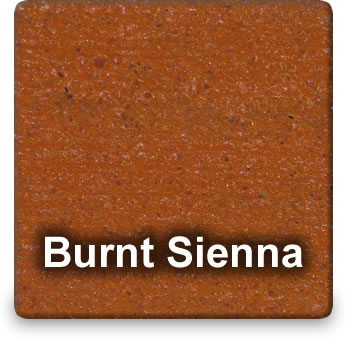
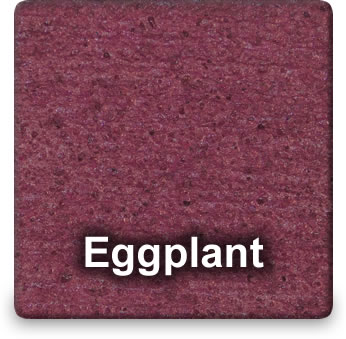
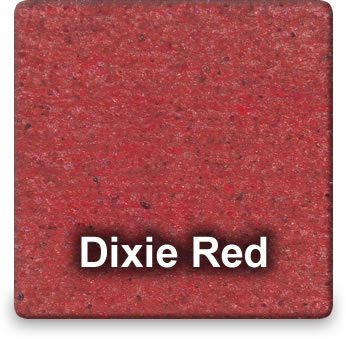
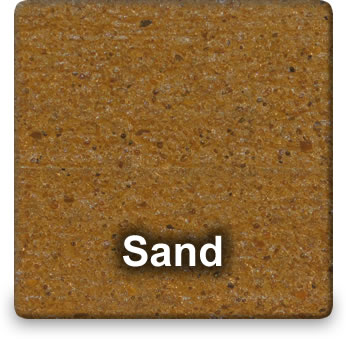
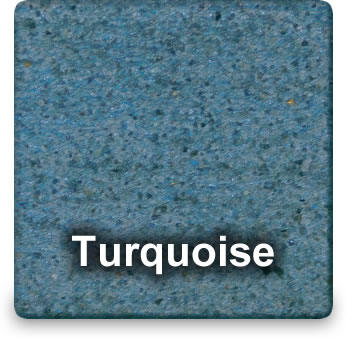
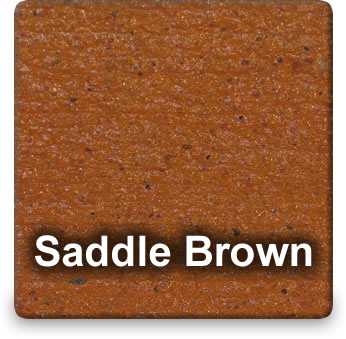
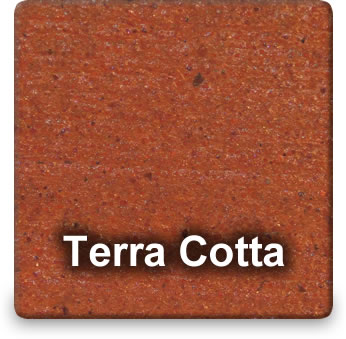
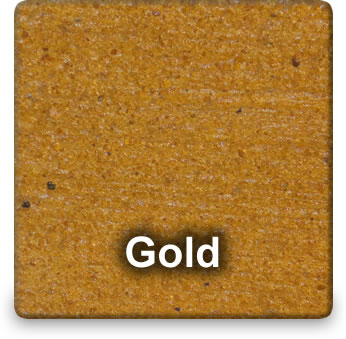
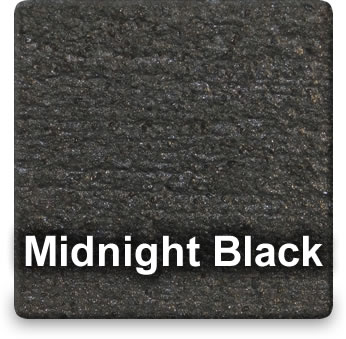
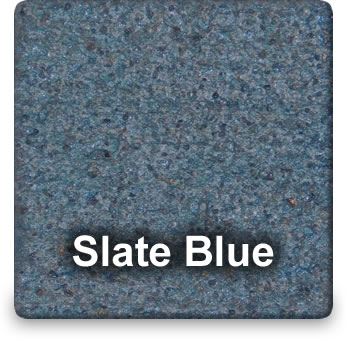
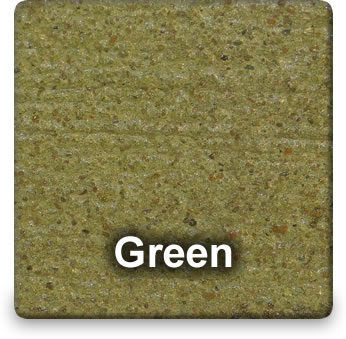

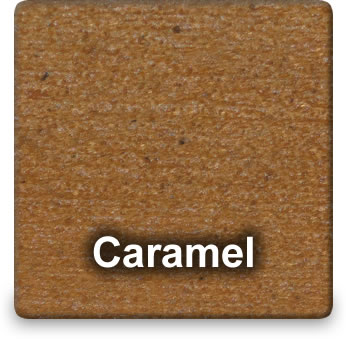
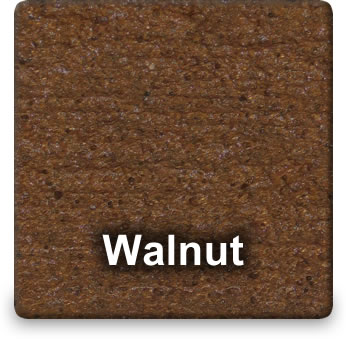
Not sure which color is right for you?
Our Exterior Kolour Dye sample sizes make it easy to choose! Sample sizes come pre-measured in convenient spray bottles ready for you to mix with acetone!
Essentials
- Extremely concentrated
- Mixes with acetone
- 28 awesome colors
- Interior or exterior use
- Must be sealed to protect color
- Spray application
- Coverage - See Detailed Info
Video showing a quick overview of the dye and seal process!
WARNING: This product can expose you to chemicals including Cumene, which is known to the State of California to cause cancer. For more information go to www.P65Warnings.ca.gov.
Detailed Info!
To learn more, keep reading or click a link below to jump to a specific topic:
- Detailed Description
- Cleaning and Preparation Instructions
- Mixing
- Application Instructions
- Sealing
- Maintenance
- FAQ's
Surfkoat Concentrated Acetone Dye
Acetone dyes are the new generation of concrete coloring products. These dyes are extremely easy to use and allow a floor staining project to now be completed in hours instead of days! Dyes are available in a huge selection of colors that can be mixed, mottled and layered to create an endless array of color and contrast options. Exterior Kolour Dye comes in a concentrated form that the label recommends to be mixed with 1 gallon of acetone, but due to it's super-high concentration we always recommend mixing each bottle with 2 gallons of acetone. This not only saves money, it makes the dye much easier to apply and reduces the risk of over-application. After application, dyes must be sealed to enhance and protect the color. Dyes should only be sealed with "film-forming" sealers which will physically "lock" in the color.
One unique challenge with acetone dye (especially on smooth interior floors) is that rolling a sealer (especially solvent-based sealers) over the dyed concrete will dissolve and lift the dye onto the roller, distorting the color and pattern you worked to create. Because of this, we always recommend that if possible, the first coat of sealer or a primer is sprayed onto the dyed surface, not rolled. Of course, this should be the preferred method anyway since it is faster, easier and creates a more even and uniform coat. This first "primer" coat will lock in the dye, making it safe to proceed with the top-coat of your choice. Dyed concrete is compatible with all types of sealers and coatings, from simple inexpensive acrylics, to high performance urethanes and polyaspartics. Be sure to choose the sealer or sealers that are right for your project and the use it will receive. If you need help, give us a call and we'll be glad to walk through the process with you. That's what we're here for!
Cleaning and Preparation Instructions
3. Interior Floors MUST be profiled prior to application. Diamond grind floors to between 50 - 100 grit. Be sure to remove all swirl marks, but do not grind finer than 100 grit. Beyond 100 grit, topcoat adhesion will be compromised.
4. Allow area to dry completely.
Mixing Instructions
WARNING: Follow the acetone manufacturer's instructions and the Safety Data Sheet for exposure limitations and safe handling practices. Acetone is HIGHLY FLAMMABLE! Do not smoke! Turn off all portable heaters and gas pilot lights. Extinguish all open flames prior to use! Avoid sparks!
PLEASE NOTE: The amount of concentrate in each container WILL vary depending on color. Each color is precisely dispersed to provide consistent results with a minimum dilution of one gallon (128 oz) of acetone per container.
Exterior Kolour Dye is packaged in a liquid concentrate form which needs to be mixed with acetone before use. Mix each bottle of Exterior Kolour Dye into appropriate amount of acetone to create the concentration and intensity desired. Each container of concentrate should be mixed with a MINIMUM of 1 gallon of acetone, but most contractors prefer further dilution to make a less concentrated dye. This will make the dye much easier to apply and reduce the risk of over-application. We recommend a typical dilution of 1 container of concentrate : 2 gallons of acetone. If you choose to dilute with only 1 gallon of acetone as the container recommends, extreme care should be taken to avoid over application. DO NOT OVER APPLY! Over applying may result in delamination. Using the re-closable acetone container is recommended for mixing. Blend the mixture by stirring the open container, or by shaking the closed container for 30 seconds. Do not use any form of electrical equipment to mix the dye with the acetone!
Tip... We have found that the lighter greens and blues (especially Lime, Teal and Turquoise) yield better results that better reflect the color chart if diluted even further than normal. Most contractors prefer to mix each container of concentrate with 3 or even 4 gallons of acetone. This allows you to build the color up slowly until you achieve the exact color you desire.
Special Considerations for Sample Sizes: Samples are without a doubt the best way to ensure you achieve the perfect desired color or combination of colors. If possible, always test on the same surface you intend to color, and then make your final decision only after observing the sample with the sealer you intend to use.
When you receive your sample size(s) of Kolour Dye, the concentrate will be dispersed into small 4-ounce spray bottles. Just like the full-size containers, these will need to be mixed with acetone before use. Following all safety precautions for working with Acetone, carefully fill each bottle almost to the top with acetone, leaving just enough air space that you will still be able to shake the contents. Securely replace the lid/pump assembly and shake contents well. For best results, allow mixture to stand for at least an hour before use to allow the concentrate to fully dissolve into the acetone. Shake well again before use or dispersing from container.
A sample size bottle filled with 4 ounces of acetone yields the same concentration as a full-size container mixed with 1 gallon of acetone. Just like with the full-size containers, we highly recommend further dilution. This will make the dye much easier to apply and reduce the risk of over-application. The easiest way we have found to do this is:
1. Mix the sample bottle with 4 ounces of acetone as described above.
2. Pour the mixture into a larger acetone resistant container.
3. Refill the sample bottle with another 4 ounces of acetone and shake well.
4. Again, pour this into the larger container already containing the first mixture.
5. Shake or stir contents to ensure they mixed well.
This diluted mixture will now yield the same concentration as a full-size container mixed with 2 gallons of acetone.
The dye can then be applied with the supplied sample spray bottle, but for best results we recommend an HVLP spray gun.
Application Instructions
Before application, always test the dye in an inconspicuous area to ensure color and compatibility are acceptable. Apply a small amount of water, observing the color while wet. This will approximate the sealed color (if using a color enhancing sealer). Concrete should be fully cured for 28 days before dyeing or sealing.
Perform moisture vapor test by taping a plastic sheet on a one square foot section of floor. Remove plastic the following day. If floor is wet, DO NOT PROCEED. First determine if moisture is remaining from the cleaning process, or if it is a more serious issue coming from the soil below the slab. If you suspect a moisture issue from beneath the slab, DO NOT PROCEED.
Protect all areas not to be stained. Mask off all adjacent surfaces. Use coated cardboard as a spray shield. Use only acetone resistant sprayers. Before opening or handling acetone and Kolour Dye, first put on proper protective equipment including eye protection, rubber gloves and respirator rated for use with acetone.
Surfkoat Kolour Dye may be diluted with additional acetone to create lighter colors if desired.
Multiple colors of Kolour Dye may be used to create any desired combination of colors, highlights and contrast. If using multiple colors, always start with the lightest color first as a base coat.
COVERAGE RATES:
Coverage rates are approximate and will vary depending on substrate density, porosity and application.
Broom Swept Concrete: One container of Kolour Dye concentrate is typically enough to color 400 - 500 sq. ft. of broom swept concrete.
If diluted with 2 gallons of acetone: Apply to concrete at a rate of 200 - 250 sq. ft. / gallon.
If diluted with 1 gallon of acetone: Apply to concrete at a rate of 400 - 500 sq. ft. / gallon
Troweled Concrete: One container of Kolour Dye concentrate is typically enough to color 500 - 600 sq. ft. of troweled concrete.
If diluted with 2 gallons of acetone: Apply to concrete at a rate of 250 - 300 sq. ft. / gallon.
If diluted with 1 gallon of acetone: Apply to concrete at a rate of 500 - 600 sq. ft. / gallon
Sealing
Allow Kolour Dye to dry for approximately 30 minutes prior to applying sealer or protective coating. If using a solvent-based sealer, the first coat of sealer or "primer" should be sprayed over the dyed surface, not rolled. Rolling may reactivate the dye and cause it to lift onto the roller.
You have many choices when it comes to choosing a sealer. Several factors including budget, durability and desired appearance will influence this decision. To give you a starting point, here are our most popular recommendations:
Interior Floors - High Performance:
First Coat (primer coat):
Polyrez 6000 WB Urethane (for enhanced color)
Polyrez 1040 WB Epoxy (for minimal enhancement)
Second Coat (topcoat):
Polyrez 6000 WB Urethane (for a gloss finish)
Polyrez 6100 WB Matte Urethane (for a matte finish)
Interior Floors - Economical:
Outdoor Concrete - Film-Forming Sealers:
Deco-Guard, StampSeal-25, 2000 Supreme, or Hurricane CAT-5
Outdoor Concrete - Penetrating Sealers:
Enhancer Shield SB (water-based version of ES should NOT be used over KolourDye. Use solvent-based version ONLY)
Be sure to choose the appropriate sealer for your application. If you need help, check out the "Help Center" or just give us a call and we'll be glad to walk through the process with you. That's what we're here for!
Of course, having the right tools will make your job easier, so scroll to the bottom to see our recommended Sprayers, Brushes and Application Tools!
Maintenance
Maintain protective top-coat according to manufacturer's recommendations.
FAQ's
Got Questions?
Check out the "Help Center", send us an email or just give us a call and we'll be glad to help you with your order!